Holcim has optimised its automated dispatch processes and weighing technology in its eastern Europe plants. Since the beginning of the year, the LOGiQ logistics software by Schenck Process has been automating all process and data management relating to dispatch services in the company's 14 locations from Slovakia to Bulgaria. Four other locations are currently in the process of being connected to the highly available dispatch automation system including all Outbound-, Inbound- and AFR transports by truck, train or ship.
New generation of LOGiQ in use
The key to the success of construction projects relies on smooth delivery of cement, explains Schenck. With the new generation of LOGiQ the cement manufacturer is able to network, manage, and document all stages of its intralogistics via Internet and Web 2.0 technology. "Quick, efficient, and most importantly insusceptible to manipulation. LOGiQ shortens waiting times, takes advantage of time, and helps save on raw materials," according to the measuring and process technologies specialist.
Automated shipping processes interlock new hardware and software components with existing ones while relying on networking local intelligence. All major components of the hardware and software modules from the LOGiQ portfolio are currently in use at the 18 Holcim locations. LOGiQ controls the workflow management system from orders receiving to printing delivery notes automatically and in the local language of Holcim's customers. All transactions between the delivery point, mixers and scales, operator terminals and loading bays are logged, stored, and archived. The orders are smoothly reported to the ERP system (SAP) without loss.
Unifying all business processes
The cement manufacturer has set itself the ambitious goal of unifying all business processes across Europe, Schenck highlights. With the help of LOGiQ and the team at Schenck Process, the phase in Eastern Europe is nearing successful completion. "We are headed in the right direction towards a smart factory," says Ionut Grosu, Head of Automation and Electrical in the Regional Support Organization Emerging Europe. The automated solution smoothly handled more than 10,000 transport orders in the 14 locations in January alone, the month it went online.
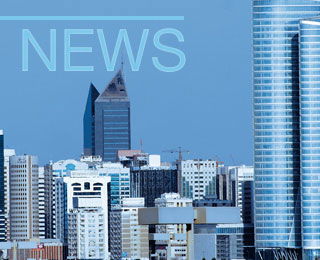
Power Cement reports positive 3Q and 9MFY24-25 results
Pakistan-based Power Cement Ltd posted PKR7.182bn (US$52.5m) in revenue for the quarter ended ...