South Africa still has barriers it needs to overcome to make alternative fuels more accessible for cement producers.
While Natal Portland Cement (InterCement group) has redesigned parts of its production process to accept several waste types, in other countries the group has a much higher alternative fuel usage. InterCement has achieved 50-70 per cent AF usage in some of its facilities, but in South Africa this is more difficult.
Inland for EnviroSer which supplies liquid hydrocarbon to the Natal cement producer explains that South Africa's waste management has not developed as fast as in other countries. Dave Morrey, general manager at Inland for EnviroSer, says: "Landfill disposal is still cheap and converting cement kilns to be able to run off waste takes a large capex investment."
Moreover, in Europe and elsewhere globally, cement kilns are often located in or very near major cities or industrial sites, whereas in South Africa these facilities are often located hundreds of kilometres away, close to lime quarries. It often requires a long journey to transport waste to cement plants to dispose of it.
In addition, there are technical challenges with using low-quality secondary fuels in South Africa. "The feeder systems in many cases cannot feed the low energy material fast enough to maintain the required temperature and therefore 100 per cent substitution is not possible, only partial substitution of some of the traditional fuel used," Dr Johan Schoonraad, EnviroServ technical specialist, told Creamer Media's Engineering News.
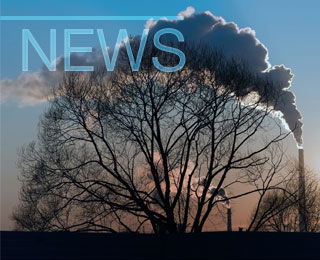
ACC's Barmana plant acts on NGT environmental warnings
ACC Ltd Cement’s Barmana plant , in Himachal Pradesh, India, has submitted a supplementary re...