TIitan Group and thyssenkrupp have signed a Front-End Engineering Design (FEED) contract for the IFESTOS Carbon Capture Project. IFESTOS is one of the largest carbon capture projects in Europe, enabling the production of zero-carbon cement and concrete.
The engineering contract provides for thyssenkrupp to design and equip the two kiln lines of the Kamari cement plant in Greece with oxyfuel systems for CO2 capture. This technology will enable the plant's CO2 emissions to be reduced almost completely. The plant is scheduled to go into full operation at the end of 2029.
“With the oxyfuel technology we have developed, around 1.9Mt of CO2 can be captured annually at the Kamari plant alone,” says Dr Cetin Nazikkol, Chief Strategy Officer at thyssenkrupp Decarbon Technologies. “This corresponds to around twelve percent of all greenhouse gas emissions from Greek industry. We are thus making a significant contribution to one of the largest CO2 capture projects in Europe.”
The captured CO2 is then liquefied and transported to a permanent storage site in the Mediterranean region. This makes thyssenkrupp’s technology the starting point for the development of important CCS value chains in southern Europe.
The signing ceremony was attended by Marcel Cobuz, Chairman of Titan Group Executive Committee, Samir Cairae, Chief Technology Officer of TitanGroup, Leonidas Canellopoulos, Chief Sustainability and Innovation Officer of Titan Group, Dr Cetin Nazikkol, Chief Strategy Officer at thyssenkrupp Decarbon Technologies and Christian Myland, CEO thyssenkrupp Polysius.
“For our customer Titan Group, we will be using the latest CO2 separation technology. We will design and equip the first kiln line with the proven oxyfuel technology. When modernising the second kiln line, the latest generation of this technology will be used with the pure oxyfuel system. Overall, this will enable us to capture almost 100 per cent of CO2 emissions,” adds Christian Myland, CEO of thyssenkrupp Polysius.
The basic principle of the pure oxyfuel technology developed by thyssenkrupp Polysius is to separate the CO2 produced in a kiln plant from the exhaust gases of cement factories and thus prevent it from being released into the atmosphere. To achieve this, pure oxygen is used in the combustion process instead of ambient air. In combination with downstream treatment, almost 100 per cent of CO2 emissions from cement clinker production can be captured.
The separated process gas is then treated to produce high-purity CO2 and can then be used as a feedstock in the chemical industry or as a raw material in other industries, or alternatively stored.
The pure oxyfuel technology was developed by thyssenkrupp Polysius, at one of four business units of thyssenkrupp Decarbon Technologies.
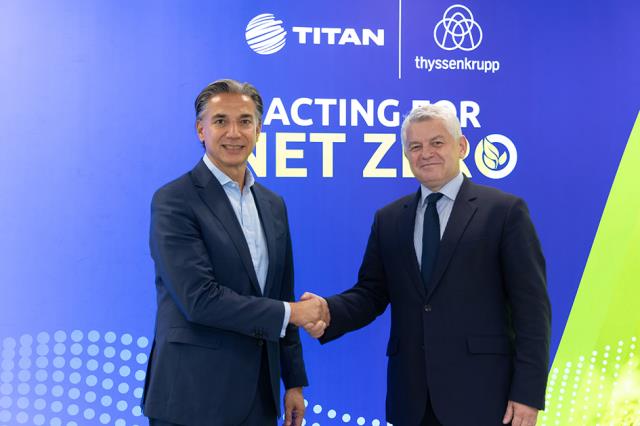
From left to right: Dr Cetin Nazikkol, Chief Strategy Officer at thyssenkrupp Decarbon Technologies
- Marcel Cobuz, Chairman of Titan Group Executive Committee