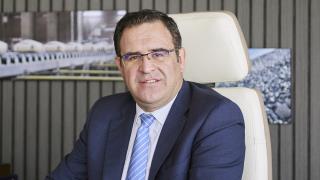
Arabian Cement's decarbonisation roadmap
With supranational developments such as the EU’s carbon border adjustment mechanism and macro-eco...
India, the world’s second-largest cement producer, is actively reducing the carbon footprint of its cement industry. On the eve of the 18th NCB International Conference and Exhibition on Cement, Concrete and Building Materials, ICR speaks with Dr L P Singh, director general of the National Council for Cement and Building Materials (NCB) about the achievements of the sector in decarbonising its operations and products.
GBP£220 / USD$315 / EUR€260 annually
Our editors pick the top news delivered to your inbox. Sign-up today!