When Li Juan took a look at European quarries last year, she was amazed by what she saw. Li, who has been a researcher at the China Building Materials Academy for more than a decade, describes her tour of the quarries as an eye-opener.
Rather than growing back grass and trees, European cement producers rehabilitate their quarries down to the last detail, including bringing back the kinds of birds and insects that used to live there, Li says.
The study tour was Li's first visit on biodiversity to Europe after she was appointed China officer of Cement Sustainability Initiative (CSI), and she is confident the gap between Chinese cement makers and their European counterparts in sustainable development will soon disappear with the help of CSI.
CSI, whose headquarters are in Geneva, is a project that helps the cement industry tackle the challenges of sustainable development. It set up an office in Beijing last June, aiming to better pass on international knowledge and expertise to China's colossal cement industry, of whose 3800 producers make more than half the world's cement.
The CEO-led programme initiated in 1999 by 10 big cement makers develops guidelines for implementing greater efficiency measures through cooperation and sharing expertise among members.
As many as 24 cement companies have joined CSI, representing one-third of the world's total output, out of which five are from China, representing 20% of China's total cement output of more than 2bnt last year.
"Since 2009, when the first three companies joined us, we've seen a growing desire among Chinese cement makers to learn how to handle sustainable development," Li says.
"The trend is in line with the development of the cement industry in China and the growing awareness of environmental protection from policy makers and companies."
Li says the focus of her job in the country is to help its current participants adhere to methods and guidelines CSI members have agreed on, such as reporting CO2 data and safety data for independent third-party verification.
But using CSI's methodologies to report those figures is a challenge for Chinese cement producers who have only latched onto the idea of sustainable development in recent years.
For example, a recent paper by Chris Nielsen, executive director of China Project with Harvard School of Engineering and Applied Sciences, estimated that CO2 emissions from the cement industry account for about one-eighth of China's national CO2 emissions.
According to Nielsen, the amount is calculated "bottom-up", based on plant-level information on "activities" such as cement production and fuel combustion and "emission factors", including the combustion CO2 emissions per unit of fuel burned and chemical CO2 emissions per tonne of limestone.
"Chinese cement makers don't have a system to do it," Li says. "They simply find out how much coal and limestone they use for the production of cement a year and then calculate a rough number.
But there is a deadline. CSI rules that all the five Chinese cement producers have to submit reports on their sustainable performance by 2013 to maintain their membership.
To help them achieve the goal, CSI's China office formed four task forces this year: in climate protection, fuels and raw materials, health and safety, and quarry rehabilitation and biodiversity. About 60 people from the five companies meet to compare notes and take part in CSI training sessions.
Zhang Zhaokun, deputy manager of China Tianrui Group Cement Co of Henan, which joined CSI in 2009, says: "I don't think our report to CSI in 2013 will look bad. After all we've spent a lot updating our equipment to reduce carbon emissions and wastewater.
"But in terms of a standardised management system we still lag behind our Western counterparts. Their approach to sustainable development is comprehensive."
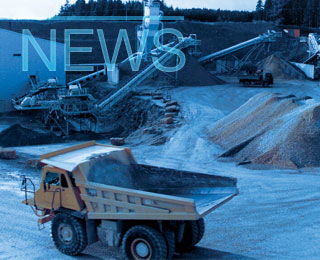
Indonesia cement demand continues to contract
Cement sales in Indonesia amounted to 3.842Mt in March 2025, a drop of 21.6 per cent YoY compare...