Following the European Commission's initiative to develop a dedicated plastics strategy in a circular economy, published on 16 January, the European cement association, Cembureau, has highlighted the part played by the cement industry in reducing plastic waste.
Apart from the importance of the need for a ban on landfill of recoverable and recyclable waste, the organisation urges policymakers to strongly focus on the recognition that cement plants can treat different waste streams such as plastics and simultaneously recycle them as material in the manufacturing process of cement and recover them as energy, helping to address the depletion of primary raw materials as well as lowering the industry’s CO2 footprint. In addition, co-processing provides "the necessary parameters for a full burnout of non-recyclable plastic waste, while also having a minimal environmental impact. As the plastic waste fuels' components, ie the mineral constituents of the ashes are entirely incorporated into the cement clinker, co-processing offers the unique opportunity of a simultaneous energy and material recovery," says Cembureau. Moreover, this approach offers the potential to minimise investment costs in dedicated facilities, which requires a huge capital investment and in which operating costs tend to be higher. Whilst high quality recycling is the preferred option, the combination of material recycling with energy recovery in co-processing is the next best solution that delivers the best overall environmental, social and economic outcome.
The Plastics Strategy must ensure that any plastic waste with calorific value that can be recovered as a fuel source must not be landfilled. At present there are considerable differences in waste management policies across the EU member states and measures on separate collection, sorting and material recovery could most likely be implemented in a cost-effective way in many member states, according to Cembureau.
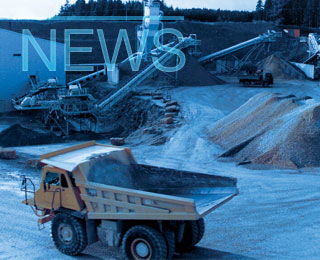
Indonesia cement demand continues to contract
Cement sales in Indonesia amounted to 3.842Mt in March 2025, a drop of 21.6 per cent YoY compare...