The research company CI4C (Cement Innovation for Climate), founded by the four cement manufacturers Dyckerhoff GmbH (Buzzi Unicem SpA), HeidelbergCement AG, Schwenk Zement GmbH & Co KG and Vicat SA, has commissioned thyssenkrupp's Polysius business unit to build a polysius® pure oxyfuel kiln system on the site of Schwenk Zement's Mergelstetten cement plant in southern Germany.
The polysius® pure oxyfuel process is a new type of clinker production process in which the otherwise normal ambient air is replaced by pure oxygen in the kiln combustion process. Compared with conventional plants, this novel process aims to concentrate, capture and reuse almost 100 per cent of the CO2 produced in a cost-effective manner. The medium-term goal is to further process the captured CO2 with the help of renewable energies, eg into so-called "reFuels", to produce climate-neutral synthetic fuels, such as kerosene for air traffic.
Advantages of polysius® pure oxyfuel technology
In the clinker burning process commonly used to date, oxygen from the ambient air supplied is used. The oxygen content of the ambient air is around 21 per cent. By using the ambient air, nitrogen in particular is introduced into the system, so that the concentration of CO2 in the exhaust gas is only about 25-30 per cent.
By introducing pure oxygen with the polysius® pure oxyfuel process, atmospheric nitrogen is eliminated from the clinker burning process. The gas volume is reduced considerably and allows a high concentration of CO2 in the exhaust gas, so that almost 100 per cent of the climate-damaging CO2 can be captured.
Complex exhaust gas recirculation, as envisaged in the first-generation oxyfuel process, can be dispensed with here. This leads to overall reduced investment and operating costs for the polysius® pure oxyfuel process.
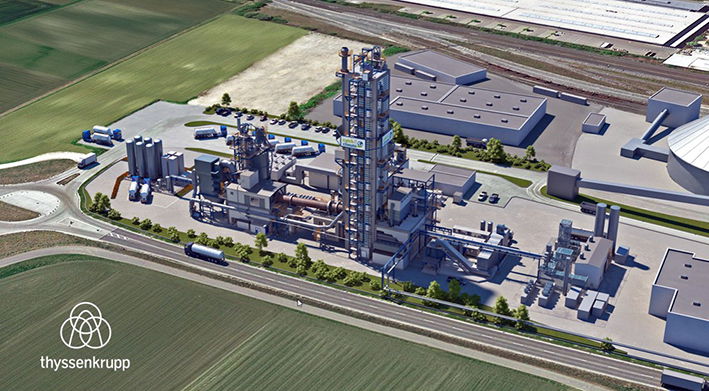
CI4C will install a Polysius® pure oxyfuel kiln system at the Mergelstetten cement plant, Germany